Problems in mold design and customization of silicone gift
Time of publication: 2021-05-03 19:23:31 browse: times edit:Silicone products manufacturers
The customization of silicone gift can not be separated from the design and manufacture of silicone mold. The thickness and width of silicone gift are determined by silicone mold. The upper limit of silicone gift mold thickness is generally 250 mm, the external size of mold can reach 500 x 500 mm, and some internal size of mold can reach 400 x 400 mm. The mold structure is generally divided into upper mold, lower mold, bottom plate, top plate, top rod, mold core, bottom plate, bottom plate, bottom plate, top rod, top rod, top rod, bottom plate, bottom plate, bottom plate, bottom plate, bottom plate, top rod, top rod When designing silicone gifts, we should pay attention to the mold characteristics and production process.
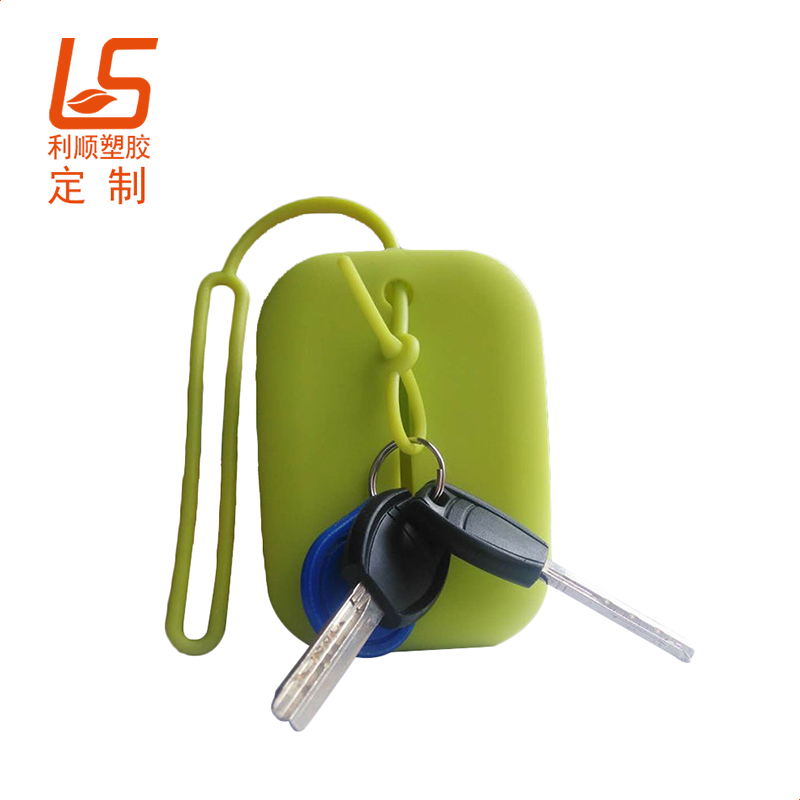
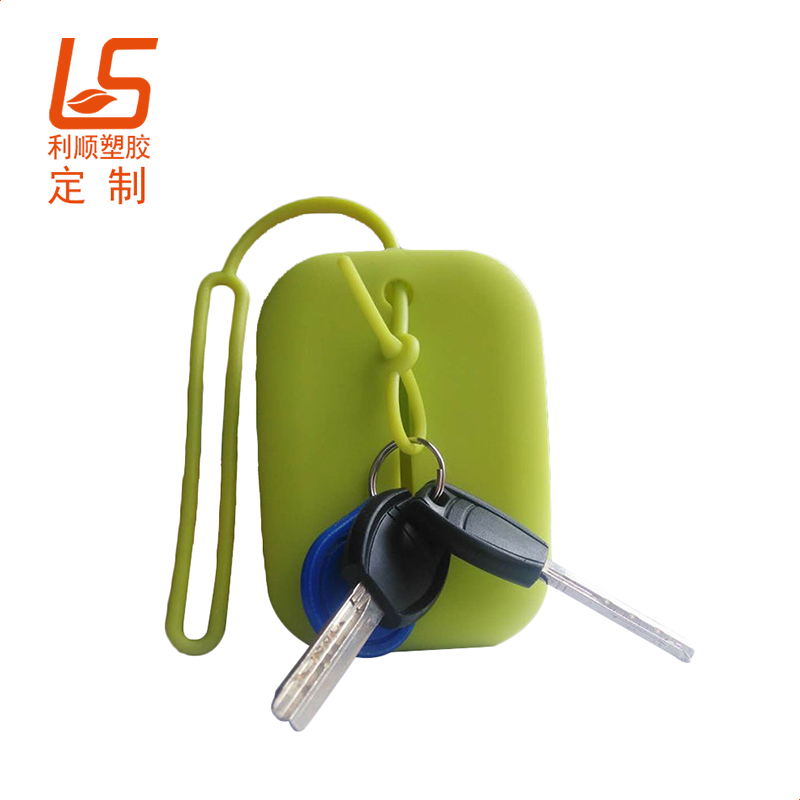
Appearance of silica gel gift: the surface of silica gel products is complete and has great toughness, but once cracks appear in silica gel products, the cracks will expand rapidly under the action of external force, that is, silica gel products are very sensitive to cracks. In view of the above problems, attention should be paid in the design of silica gel gift parts: each part should not have sharp corners to avoid cracks caused by stress concentration, and the R angle of opening should not be less than 0.5mm.
The first mock exam of silicone products is that it can not automatically walk, but it can be removed. It is only suitable for small size structure. The core pulling device is similar to plastic mold, but it needs to be removed manually when opening the mold. Besides, core pulling takes up larger space of mold. In a silicone mold with more than one mold, it is not only complicated in processing but also low in utilization rate of mould space, so try not to pull core.
Demoulding of silica gel products: the silica gel products can be demoulded directly, and the size requirements for the strong demoulding of silica gel products without design defects are mainly the perimeter ratio of the larger part of the mold core to the closing part during demoulding, which is less than 55 ° The product can be 2-3 times, and there should be no cracks and sharp corners at the opening where forced demoulding is needed. Due to the need for curing temperature above 180 ℃, in addition to the upper and lower mold separate, demoulding work almost all by hand. So in the design of parts, we should consider the convenient separation. Avoid the influence of too long demoulding time on the vulcanization quality and production efficiency of parts. Because the demoulding method of silicone gift is mainly manual, the movement stroke of the top plate is also very small, so the silicone gift mold has no inclined top compared with the plastic mold. Generally, core pulling is not set. Different from plastic mold, the core of silicone gift mold is usually removed together with the product parts when the mold is opened. Therefore, it is more difficult to fix and accurately position the core than the plastic mold, which requires higher rigidity of the core. Generally, they are made together and all modules are installed at one time. Or through the auxiliary device, the model can be positioned quickly. Due to the large pressure in the process of clamping, it is necessary to strictly prevent the movement of the mold core.
Silicone accessories inlay: silicone gift manufacturers can inlay various types of inlay, but need to pay attention to: first, the surface of the inlay part should be pretreated, mainly surface vulcanization or surface activation. Otherwise, it will be difficult to connect the insert and the adhesive firmly. Secondly, the positioning of the insert can be unidirectional in the vertical direction, but it must be comprehensive in other directions. Avoid insert movement during full mold processing. Third, the thickness of the adhesive layer around the insert. For fully glued parts (all surfaces are glued, so it is not possible to position the insert), there should be at least 0.5mm glue thickness around the insert.
For positioning inserts, the thickness of the surrounding adhesive layer should be greater than 0.4 mm.
Dumper side of mould: the main function of dumper side is to hold too much adhesive, which is convenient for discharging mould and cleaning flash. In general, the self dismantling edge is composed of a circle of thin edges on the parting surface and relatively firm tearing edges. The thickness of thin edge is generally 0.1 ~ 0.2 mm, the thickness of tearing edge is generally 0.8 mm, and the width is generally 1 ~ 2 mm.
(This article is edited and original by Lishun silicone gift. Please indicate the source for Reprint:www.lishun666.com)